Osnai: plastic injection machine unit is easy to damage, 6 aspects must be paid attention to!
publishtime:2021-12-06 丨 Read the number:1388
Osnai: plastic injection machine unit is easy to damage, 6 aspects must be paid attention to!
Plastic components of injection molding machine, here refers to: screw, plastic cylinder, rubber head, rubber ring, rubber washer.
When the injection molding machine is working, the plasticized component is like the wheel of a motor vehicle. As long as it starts, it will be subjected to pressure, impact, friction and extrusion. For the same tire, driving on flat road, skilled driver operation, often can prolong the service life of the tire. And often in uneven, gravel more road driving, coupled with regular emergency brake action, tire tread pattern will soon be ground flat, scrapped.
Therefore, in order to ensure that the injection molding machine is always in good condition, it is necessary to clarify the performance of the injection molding machine, understand the performance and quality of the plastic materials used, strengthen the management of the use of injection molding machine, in order to reduce the failure rate, reduce maintenance costs, prolong the purpose of service life.
Generally speaking, the service life of plasticizing system of injection molding machine is affected by the following aspects:
1. Mechanical wear
Some modified plastics added minerals, glass fiber, metal powder, etc., the existence of these materials, in the process of plasticizing and injection processing, will accumulate over a long period of time to screw, three small pieces and melt plastic cylinder for uniform mechanical wear. Nitriding layer can be ground off, chromium plating layer. After wear, the gap between the screw and the melt cylinder increases, which reduces the plasticizing effect, increases the leakage of the injection, reduces the injection efficiency and reduces the processing accuracy.
Therefore, in order to minimize wear and prolong the service life of plasticized components, the temperature should be appropriately raised during processing and the screw speed should be reduced. Choose chrome plating or bimetal scheme, can more effectively prevent wear.
2. Mechanical fatigue and overload operation
Tuner personnel habitually set low temperature work, habitually set high speed and high pressure work, so that the performance of plasticized components gradually deteriorate.
For example, PC, PA plastic processing, in the temperature does not meet the requirements, plastic viscosity is very large, if the sol action is forced at this time, we must increase the sol pressure, increase the sol torque, thus increasing the stress fatigue of the screw.
At the same time, because the viscosity of the plastic melt is very large, it is necessary to increase the injection pressure and injection speed for injection molding, increasing the impact and load of the three small parts, accelerating its wear and stress fracture.
3. Human factors (including operation errors or illegal operations)
· When metal impurities are mixed into the plastic melt cylinder together, the screw edge, groove, rubber ring and rubber washer of the screw will be worn to different degrees due to extrusion, resulting in unstable injection molding and easy to produce black spots and black lines;
· Add wrong plastic artificially, add high temperature plastic to the melt tube set at low temperature, resulting in excessive torque of the screw during sol, resulting in stress fatigue of the screw;
· Cold start is a kind of anxious psychology and irresponsible working attitude. In sol barrel temperature temperature or just meet, do not meet the set requirements of residual material in pipe, absorbed in its outer heat from hot coil temperature is higher, and the inner temperature is still very low, so the cold start when the screw torque is large, make the screw produces stress fatigue, serious twist off the screw quickly, twist off the plastic head and the aprons.
· Most of the metal impurities entering the sol cylinder are brought in with the crushing material. Therefore, it is necessary to check the breakage of the crusher blade frequently, and replace the blade immediately if it is found to be worn.
On the other hand, the magnet in the hopper should be regularly checked and cleaned. When the magnet around the absorption of metal filings saturated, for the outer layer of iron filings will be weakened, even if sucked, it is easy to be constantly flowing plastic washed away, together into the sol cylinder.
4. Correct assembly, adjustment and replacement of parts
This aspect is also very important, if the assembly of sol cylinder fashion is not tight enough, sol or glue shooting action will appear when the screw touching sol cylinder phenomenon, resulting in screw or sol cylinder wear. Therefore, it is necessary to check the technical status of the equipment regularly and pay attention to the abnormal phenomena in the processing of parts.
5. Damage caused by improper process
· Long-term use of high back pressure sol can accelerate the wear of three small plasticized parts. This situation generally occurs in the use of toner, because toner is difficult to disperse, so the method of increasing back pressure is adopted.
· For plastics with high viscosity, quick sol is used for sol, which causes stress fatigue of screw;
· High speed sol method should not be used for high temperature plastics, especially for plastics with glass fiber.
6. Chemical corrosion
The corroded metal is made of iron. Common corrosive plastic: flame retardant plastic, acid plastic, PVC plastic and so on. Screw, melt cylinder and flange are corroded, the surface of some pits, rough surface, so that the injection molding machine working melt flow resistance.
Some materials tend to adhere to the surface and cause decomposition carbonization. Severe corrosion causes the gap between the screw and the melt cylinder to become larger, the leakage increases, so that the injection efficiency is reduced.
From flame-retardant plastics to acid adhesives, plastics break down acidic gases when processed at high temperatures, and the melt easily carbonizes and sticks to the metal.
conclusion
On the one hand, plasticizing components should be made of stainless steel or chrome plating.
The second aspect in the production and processing should try to use low back pressure, low temperature and low shear process, reduce the degradation of plastic;
Third, due to the thermal sensitivity of the above plastic, too high temperature or too long heating time are easy to cause the decomposition and degradation of plastic and carbonization, so the production process should avoid and reduce artificial shutdown without reason.
If you need to stop, you should first reduce the temperature, close the material gate, the melt in the sol cylinder is finished, and then switch to PP material or PS material to clean the sol cylinder.
Osonite New Materials Co., Ltd. is a professional company focusing on r&d, design, production and sales of mechanical core motion parts and related new materials. The main products are injection molding machine, extruder, rubber machine and other plastic machine screw barrel plasticizing components (screw, pipe, flange, nozzle, three small pieces), alloy steel sleeve copper sleeve, pin shaft drive shaft and so on, and provide customers with relevant professional system solutions and technical services.
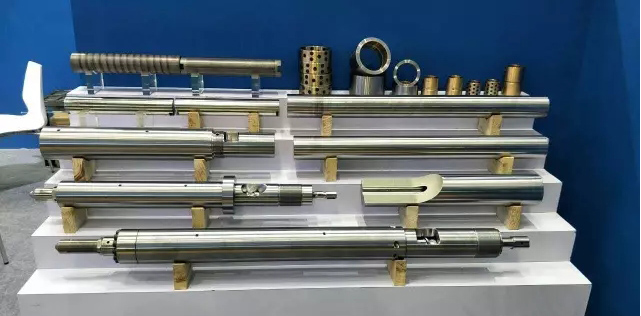
The rope has established custom resistance ability and will continue to carry forward the company's core development philosophy of "spirit, lean production, devotes to the high and new material technology was applied to improve the human daily life, the cable resistance to exalt the humanistic ideas, to explore science and technology law, spirit, innovation of enterprise culture, continue to open, communication," "Cultivate oneself and people" to consolidate the scientific and technological foundation, humanistic spirit, conscience, to provide customers with systematic solutions.
Telephone: 0769-81218861
24-hour service hotline: 4007-566-899
WeChat: 180-2917-6361
Marketing Department email: dgosnai@163.com
Website: http://www.osnai.com
Address: 86, Longxiang Ge Street, Chaolang Village, Chashan Town, Dongguan City