Roll Manufacturing Division
Focus on roller products, professional roller manufacturing, and quality assurance
Osonai Company has been specializing in roller manufacturing, introducing German technology and specializing in the production of various rubber rollers, aluminum rollers, and customized non-standard rollers for industrial use. The company has advanced processing equipment at home and abroad, including CNC lathes, milling machines, high-frequency heating machines, automatic welding machines, CO2 protection welding machines, polishing machines, mirror polishing machines, grinders, mixing machines, fully automatic winding and wrapping machines, automatic glue filling machines, vulcanization tanks, medium and high grinding machines, high-precision cylindrical grinders, dynamic balancing machines, etc. We have advanced experimental and testing equipment, as well as strict testing procedures.
Osonai specializes in the production and manufacturing of steel rollers, including tungsten carbide rollers, quenched rollers, chrome plated rollers, stainless steel pipes, aluminum rollers, anodized aluminum rollers, mirror rollers, tension rollers, fixed guide rollers, flattening rollers, guide rollers, driving rollers, driven rollers, clamping rollers, pinch rollers, roller bodies, knife groove rollers, flattening rollers, roller sleeves, auxiliary rollers, corona water cooling rollers, conductive rollers, ceramic rollers, conveyor rollers, PTFE rollers, ceramic rollers, heating rollers, mesh rollers, etc;
Rubber rollers: hydrogenated nitrile rubber rollers, polyurethane rubber rollers, carbon fiber rollers, composite material rubber rollers, EPDM rubber rollers, silicone rubber rollers, fluororubber rollers, butyl rubber rollers, natural rubber rollers, chloroprene rubber rollers, wool rollers, oil extrusion rollers, anodized aluminum rollers, functional rollers, etc;
Various types of rollers are widely used in industries such as lithium batteries, aluminum processing, metallurgy, papermaking, packaging, leather, printing and dyeing, textiles, films, plastics, and construction machinery. It can meet customers' requirements for wear resistance, high temperature resistance, oil resistance, solvent resistance, high pressure resistance, high speed, acid and alkali resistance, and can be customized according to drawings and samples.
1. Excellent wear resistance
The wear resistance of polyurethane is about 3-5 times that of natural rubber, making it suitable for high friction environments (such as printing and papermaking machinery) and significantly extending its service life.
2. High elasticity and tear resistance
Wide range of elastic modulus (Shore A50-A96), customizable softness and hardness, strong absorption of impact force, and avoidance of equipment vibration damage.
3. Oil resistance and chemical stability
Has good resistance to mineral oil, solvents (such as gasoline, lubricants), and weak acids and bases, suitable for chemical and ink environments.
4. Wide temperature adaptability
The working temperature range is usually -30 ℃ to+80 ℃, and some modified formulations can reach up to 120 ℃, which is better than most rubber materials.
5. Flexible customized design
Different hardness, color, conductivity and other requirements can be met by adjusting raw materials (such as TDI/MDI/PPD system) and processes (casting/hot pressing).
Main application areas
Steel and Metal Processing/Printing Industry/Paper and Packaging/Textile Printing and Dyeing/Steel and Metal Processing/Plastic Film and Electronics Industry/Other Industrial Fields
For example, the aluminum foil rolling mill, slitting machine, rewinding machine, and flattening roller on the rewinding machine during the aluminum foil processing; Support rollers and working rollers for cold rolling and hot rolling processes, transmission rollers for pickling lines, coating rollers for galvanizing/color coating lines, straightening rollers for straightening machines, and guide rollers for slitting machines;
Ink transfer rollers and ink equalization rollers for offset printing machines, embossing rollers and back pressure rollers for gravure printing machines, coating rollers and transfer rollers for composite machines, tension control rollers and correction rollers for slitting machines, etc
Polyurethane rubber rollers are gradually replacing traditional metal and rubber rollers and becoming the preferred component for high-precision industrial equipment through continuous improvement in material science, such as nanofiller reinforcement. When selecting, it is necessary to consult professional manufacturers for material optimization based on specific working conditions.
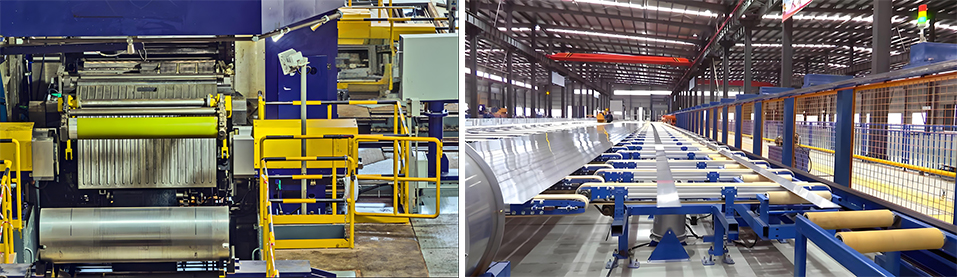
|